Boost Your Assembly Line: Aluminum Casting Approaches That Supply Outcomes
Boost Your Assembly Line: Aluminum Casting Approaches That Supply Outcomes
Blog Article
Mastering Light Weight Aluminum Casting: a Deep Study the Numerous Techniques Available
From the conventional approach of sand casting to the complicated procedures of financial investment casting and pass away spreading, each technique provides special challenges and advantages. In this expedition of light weight aluminum casting strategies, we will certainly lose light on the complexities of each technique, giving insights that might reinvent your strategy to aluminum casting.
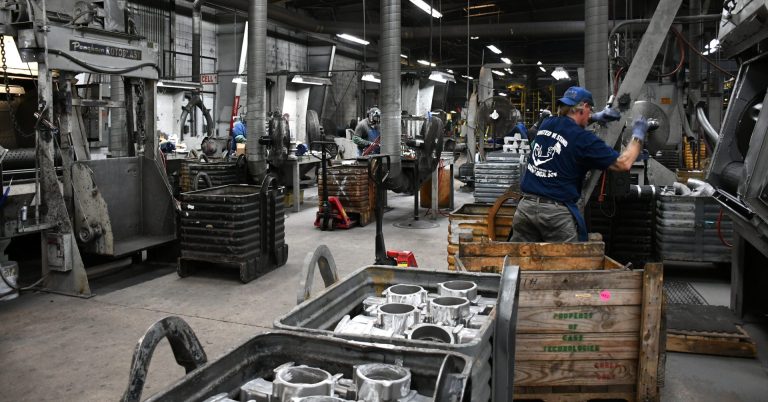
Sand Casting Technique Review
The Sand Spreading technique's versatility and prevalent application make it a foundation in mastering light weight aluminum casting processes. This strategy includes creating a mold and mildew from a mix of sand and a binder, such as clay, to create complex shapes for casting liquified aluminum. Sand spreading is a preferred selection due to its reasonably inexpensive, simplicity of modification, and capacity to produce intricate geometries with high precision.
The procedure begins with the production of a pattern, usually made of timber or steel, which is pressed into the sand to produce a mold and mildew tooth cavity. As soon as the pattern is eliminated, the mold and mildew cavity is loaded with molten light weight aluminum, which strengthens to take the shape of the pattern. After cooling down and solidification, the sand mold and mildew is broken away, exposing the light weight aluminum casting.
Sand spreading is widely utilized in numerous industries, including auto, aerospace, and manufacturing, because of its adaptability in producing both little and huge aluminum elements (aluminum casting). Its flexibility to intricate styles and cost-effectiveness make it a preferred selection for numerous aluminum spreading applications
Irreversible Mold Casting Process Described
Discovering the details of light weight aluminum spreading, the Long-term Mold Casting process provides a refined method for creating high-quality components with accuracy and performance. Unlike sand spreading, long-term mold casting makes use of a multiple-use mold and mildew normally made of steel or iron to shape the molten aluminum.
Irreversible mold and mildew casting can be categorized right into 2 main types: gravity spreading and low-pressure casting. Gravity casting involves pouring the molten metal right into the mold and mildew utilizing gravity, while low-pressure casting makes use of reduced pressure to load the mold and mildew tooth cavity. Both methods supply benefits in terms of reducing porosity and boosting mechanical buildings.
Pass Away Casting: Advantages and Negative Aspects
Understanding the ins and outs of die casting involves comprehending its distinct benefits and drawbacks in the world of light weight aluminum component manufacturing. Pass away casting offers several advantages that make it a popular option for producing light weight aluminum components. One crucial benefit is the high-speed production capacity of die casting, permitting the automation of intricate shapes with limited resistances. Furthermore, pass away casting offers exceptional dimensional precision and smooth surface finishes, lowering the need for extra machining procedures. The process is likewise very repeatable, guaranteeing regular quality across huge manufacturing runs.
Nonetheless, die spreading does include its own set of drawbacks. One significant downside is the high first tooling cost connected with producing the dies utilized at the same time (aluminum casting). These mold and mildews can be pricey to generate, making pass away casting much less economical for small production runs. The process is not as versatile when it comes to create modifications compared to other casting methods like sand casting. Despite these limitations, the benefits of die spreading usually surpass the negative aspects, making it a recommended choice for numerous aluminum casting applications.
Investment Casting Advantages and applications
Structure on the advantages of die spreading, financial investment casting supplies a flexible technique for producing detailed aluminum components with special benefits in numerous applications. Financial investment casting, additionally referred to as lost-wax casting, succeeds in producing complex forms that would be hard or difficult to achieve via other approaches. This method is widely used in sectors such as aerospace, automobile, and precious jewelry making.
Among the essential other advantages of investment spreading is its ability to create near-net form parts, decreasing the requirement for added machining and decreasing product waste. This results in expense financial savings and faster production times contrasted to typical machining processes. Furthermore, financial investment casting enables for the manufacturing of get rid of exceptional surface area finishes and tight resistances.
In the aerospace industry, investment spreading is preferred for its ability to create light-weight yet strong elements critical for aircraft performance. The auto sector take advantage of financial investment spreading for generating components with high dimensional accuracy and complex layouts. Overall, investment casting uses a specific and website link affordable remedy for making intricate aluminum parts across different industries.
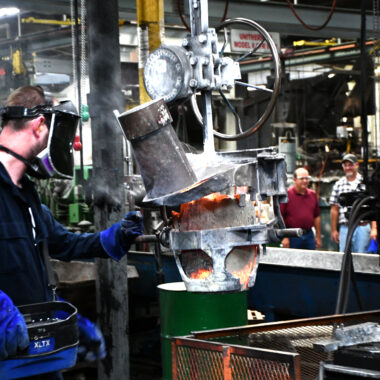
Lost Foam Casting: Just How It Functions
Shed foam casting, additionally understood as evaporative-pattern casting, is an approach for creating detailed metal parts by utilizing foam patterns that vaporize during the spreading process. This strategy starts with a foam pattern of the wanted part being positioned into unbonded sand. The foam pattern is commonly coated with a refractory product to improve the surface coating of the final steel component. When molten steel is poured into the mold and mildew, the foam vaporizes because of the warmth, leaving behind a dental caries that is then filled up by the steel.
One of the crucial benefits of lost foam casting is its capability to generate complex shapes with elaborate information that might be testing to achieve with other casting techniques. In addition, the procedure can be cost-effective as it top article gets rid of the requirement for cores and enables the consolidation of several components right into a single part. It requires careful control of the process criteria to make certain correct foam evaporation and steel circulation.
Conclusion
To conclude, mastering light weight aluminum spreading includes understanding and utilizing various strategies such as sand spreading, long-term mold spreading, pass away casting, investment spreading, and shed foam casting. Each technique has its very own advantages and applications in the manufacturing procedure. By acquainting oneself with these different approaches, makers can select the most ideal casting technique for their details requirements and requirements, inevitably bring about successful and efficient production of light weight aluminum elements.
From the traditional approach of sand casting to the facility processes of investment spreading and die spreading, each technique offers distinct obstacles and advantages. In this expedition of aluminum spreading methods, we will certainly drop light on the details of each technique, providing understandings that could reinvent your approach to aluminum spreading.
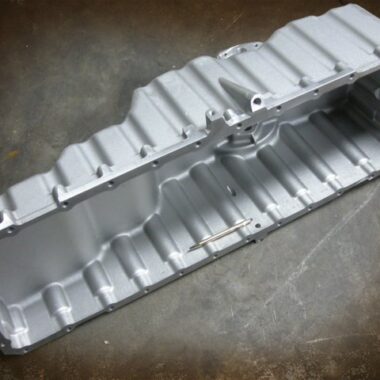
Report this page